詳細(xì)說明
傳統(tǒng)外墻粘貼式輔助保溫作為“穿棉襖”式的補(bǔ)救性保溫形式,在推廣應(yīng)用過程中出現(xiàn)了“畸形”發(fā)展,存在著以下主要弊病:
1)空鼓、開裂、滲水、脫落等質(zhì)量問題嚴(yán)重,造成了眾多“繃帶”墻;
2)可燃性保溫材料加無法全程監(jiān)管的現(xiàn)實(shí),使建筑火災(zāi)安全隱患突出;
3)外保溫?zé)o法實(shí)現(xiàn)保溫與建筑物同壽命,且二次維修的費(fèi)用沒有來源。
4)脫落時(shí)對(duì)居民人身財(cái)產(chǎn)的傷害隱患,砸車傷人事件時(shí)有發(fā)生;
5)脫落后的建筑垃圾無法有效處理,造成巨大的社會(huì)問題;
住建部2011年《“十二五”建筑節(jié)能專項(xiàng)規(guī)劃》
到“十二五”末,城鎮(zhèn)新建建筑執(zhí)行不低于65%的節(jié)能標(biāo)準(zhǔn),鼓勵(lì)北京、山東等有條件的地區(qū)實(shí)施節(jié)能75%的節(jié)能標(biāo)準(zhǔn)。
七星實(shí)業(yè)公司突破傳統(tǒng),創(chuàng)新工藝、設(shè)備自動(dòng)化程度高、實(shí)現(xiàn)閉環(huán)式循環(huán)生產(chǎn):
1.儲(chǔ)料和自動(dòng)計(jì)量:實(shí)現(xiàn)精確計(jì)量,減少人工避免物料浪費(fèi),全封閉運(yùn)行,減少環(huán)境污染;
2.PLC電腦控制混凝土下料系統(tǒng):確保均勻布料,下料準(zhǔn)確,實(shí)現(xiàn)產(chǎn)品密實(shí),避免大氣泡出現(xiàn)導(dǎo)致產(chǎn)品質(zhì)量不穩(wěn)定;
3.全自動(dòng)生產(chǎn)線運(yùn)行系統(tǒng):
A、摩擦動(dòng)力輪驅(qū)動(dòng),實(shí)現(xiàn)各個(gè)環(huán)節(jié)和工序的獨(dú)立操控;
B、摩擦動(dòng)力輪實(shí)現(xiàn)正反轉(zhuǎn),便于維修和故障排除,與傳統(tǒng)汽缸硬頂?shù)男问较啾龋Σ羷?dòng)力輪實(shí)現(xiàn)軟連接,避免破壞性生產(chǎn)事故;
C、自動(dòng)限位與電控:實(shí)現(xiàn)各個(gè)模具的自動(dòng)化運(yùn)轉(zhuǎn);
D、鏈板輸送機(jī)與升降平臺(tái):實(shí)現(xiàn)模塊的自動(dòng)擺渡,實(shí)現(xiàn)循環(huán)式緊湊性生產(chǎn),使廠房利用更合理,大幅節(jié)省廠房空間,有效減少前期廠房投資;
4、生產(chǎn)線自動(dòng)脫模系統(tǒng):
A、精準(zhǔn)定位:系統(tǒng)通過限位和電控以及機(jī)械定位系統(tǒng),自動(dòng)將模具傳送至脫模系統(tǒng);
B、整箱脫模:系統(tǒng)可以自動(dòng)實(shí)現(xiàn)整箱36塊脫模,一次性整箱脫模數(shù)量為行業(yè)內(nèi)最大。
快速高效:
5、高位升降系統(tǒng):高位升降系系統(tǒng)自動(dòng)將切塊疊成多層,轉(zhuǎn)運(yùn)到到切塊養(yǎng)護(hù)車間,單位時(shí)間內(nèi)實(shí)現(xiàn)更多切塊運(yùn)轉(zhuǎn),大幅提升運(yùn)轉(zhuǎn)效率;
6、自動(dòng)清洗與覆膜系統(tǒng)
脫模后的磨具自動(dòng)進(jìn)入清洗流程,采用行業(yè)首創(chuàng)的用雙排多頭高壓噴淋沖洗,全方位無死角,5秒清洗完畢;同時(shí)磨具底托自動(dòng)覆膜,實(shí)現(xiàn)磨具底托免清洗化,減少人工投入、減少生產(chǎn)工序;
7、雙排或多排整體保溫芯體
行業(yè)首創(chuàng)一體化整體保溫芯體,實(shí)現(xiàn)了芯體的精準(zhǔn)定位,同時(shí)實(shí)現(xiàn)保溫外殼與芯體的無縫連接,減少人工,提高效率。
8、自動(dòng)多層預(yù)養(yǎng)系統(tǒng)
模具澆筑后自動(dòng)進(jìn)入預(yù)養(yǎng)倉,多層立體化的預(yù)養(yǎng)倉節(jié)省了大量的空間,實(shí)現(xiàn)一次性大批量砌塊預(yù)養(yǎng);
9、自然熱能養(yǎng)護(hù)線
生產(chǎn)線廠房設(shè)計(jì)利用太陽光的力量進(jìn)行自然養(yǎng)護(hù),比傳統(tǒng)蒸養(yǎng)形式大幅節(jié)省能源消耗,更有利于項(xiàng)目立項(xiàng)階段的環(huán)評(píng)審批,復(fù)合發(fā)改委對(duì)于新型綠色建材的節(jié)能標(biāo)準(zhǔn);
10、自動(dòng)化程控多排轉(zhuǎn)運(yùn)車
轉(zhuǎn)運(yùn)速度快、操控性好,單次轉(zhuǎn)運(yùn)可以轉(zhuǎn)運(yùn)砌塊3個(gè)立方以上,單次轉(zhuǎn)運(yùn)量為行業(yè)內(nèi)最大;
11、自動(dòng)化成品碼垛系統(tǒng)
系統(tǒng)實(shí)現(xiàn)自動(dòng)化5層碼垛,提高了碼垛效率,節(jié)省人工,便于成品快速運(yùn)離廠房,提高生產(chǎn)效率。
12、底托自動(dòng)電磁吸附轉(zhuǎn)移系統(tǒng)
系統(tǒng)采用先進(jìn)的電磁吸附技術(shù),將底托自動(dòng)吸附轉(zhuǎn)運(yùn)至生產(chǎn)線上,實(shí)現(xiàn)自動(dòng)流水化循環(huán)生產(chǎn);
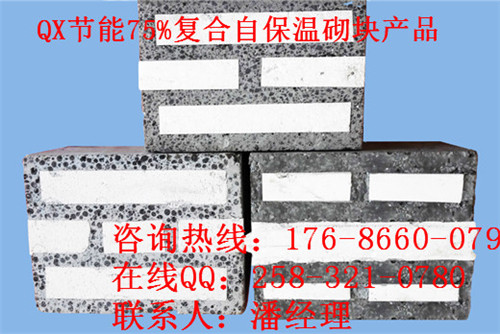
QX高性能復(fù)合自保溫砌塊采用全自動(dòng)閉環(huán)式生產(chǎn)流程,采用模箱成型混凝土澆筑生產(chǎn)工藝,雙排保溫層先在模箱中定位,然后整體濕料澆筑高性能混凝土外殼,通過生產(chǎn)工藝使砌塊殼體與保溫材料注塑成整體而形成的集建筑圍護(hù)與保溫功能一體的混凝土自保溫砌塊。QX高性能混凝土復(fù)合自保溫砌塊采用斷橋結(jié)構(gòu)設(shè)計(jì),可阻斷和有效減小砌縫處熱橋部位熱量損失,梁、柱等熱橋部位采用永久性復(fù)合保溫板進(jìn)行現(xiàn)場(chǎng)澆注成型,滿足建筑節(jié)能75%及以上的建筑節(jié)能要求,實(shí)現(xiàn)了保溫與結(jié)構(gòu)同壽命的目的。